Passive Fire Protection Update
Intumescent Coating Code of Practice Rev 2.0. A revision 2.0 of the Intumescent Coatings Code of Practice is about to be released.
As I sit here and write this Revision 2.0 of the Intumescent Coatings Code of Practice is about to be released. I’ve sighted a draft & only minor edits required before release.
Previously there had been some commentary from the wider market that the CoP was creating issues for designers to achieve their desired outcome. This was to be expected because NZ was designing & building to lazy non-compliant habits that didn’t align with the remainder of the world.
I’ll attempt here to provide some tips & tricks for users so that compliance with the CoP is achieved and it isn’t a difficult task:
Common complaints received were:
- Who is supposed to take the lead on all of the Intumescent design?
- Why can’t we install timber over Intumescent paint & difficulty achieving clearances
around paint? - Sequencing & Construction phase weather protection
Responsibility for design:
The CoP suggests that this should be a collaborative effort between all design consultants to ensure all aspects are considered. This way of thinking is no different to any other collaborative effort in designing a building whereby multiple consultants need to talk & collaborate on a solution.
The Fire Engineer will have a role in stipulating the fire rating requirement.
The Structural Engineer will have a role in stipulating which members need protection and limiting temperatures etc and likely give opinion on paint specifications as this overlaps with their corrosion considerations.
The Architect will have a role in that they can decide if the best solution is Intumescent Paint, or other form of protection such as Board encasement, Cementitious. Or it may even be possible that the Structural Engineer is able to achieve inherent protection with no fire rating system at all. The architect & Structural Engineer may consider having structural members off partition lines so that there aren’t as many clashes.
All of these considerations have fire, structural, aesthetic, buildability & cost considerations. There are also Design & Build Contractors, Early contractor engagement, Manufacturers & Engineering firms that will take a lead role on coordinating or advising on all of the above. This is occurring more & more on large scale projects where complexities and costs challenging.
Whatever the make up of your design team and project is it is recommended that at least start in the preliminary design stage with discussions regarding Post Fire Structural Steel protection – this will save a lot of problems later on.
Rev 2.0 elaborates in more detail on designer roles/ responsibilities and has added in a role of “Structural Fire Engineer” & “Design and Build contractor” which represents what is happening in the market.
Timber blocking & Clearances:
One of the debates on this version of the CoP was whether or not to remove the statement regarding blocking & obstructions over Intumescent paint as there is available proof of concept testing and literature in the market that claims this is not an issue. However, Rev 1.0 of the CoP stated to avoid timber blocking over Intumescent paint unless manufacturer has specific testing. Therefore, there has been a work around since Rev 1.0.
The first release of the CoP has encouraged many manufacturers/ distributors within NZ to go and commission their own small-scale testing to show how their paint performs when obstructed by timber or other member. These tests have been varied in their make up & what test methodology they follow.
The reality of these tests are:
- They have not been completed in accordance with BS476 or AS1530.4 – therefore they are not tests that fully satisfy NZBC. They are however good proof of concept evidence.
- The build methodology varies between how these have been compiled. Some have timber fixed to the steel, some have timber fixed around the steel, some have plasterboard. They are good evidence showing the performance indicatively though
- It is not possible to test every steel member with every type of construction obstruction
that could occur.
On two of the more robust small scale tests I have seen it is demonstrated that 30 minute & 60 minute timber obstructions & other obstructions do not impact on the intumescent performance of the paint in protecting the limiting temperature of the steel. However, over 60 minutes there is evidence that the obstructions do inhibit the properties of the ICS
protecting the steel. Hence why the rest of the world builds and designs their buildings to avoid such obstructions.
I believe at this point that every manufacturer/ distributor of Intumescent Paint in NZ market has available some form of small-scale testing proving some obstruction is ok. Therefore, open dialogue with these manufacturers/ distributors and get their literature so you Engineers can assess & consider what is appropriate for your project.
These tests are not full satisfaction of NZBC therefore they should be included as part of your Building Consent submission as an Alternative Solution. The Alternative Solution application to the BCA should provide the evidence and limitations & support from the Manufacturer and Engineers for the project.
Clearances – unfortunately, many people have interpreted that 50mm clearance is required around all Intumescent Paint. In actual fact it is 50 x the DFT. Therefore, in NZ where we often have particularly low Fire ratings for structure the DFT is often much lower than 1mm.
We would suggest where clearances are particularly tight do some quick calculations against the loading schedule & you’ll likely be pleasantly surprised that required clearances are as low as 10 – 25mm – 37mm.
Sequencing & Construction Phase protection:
The single biggest mindset change that I can suggest is that you need to consider Intumescent Paint as a
Structural phase trade, not a fit-out trade. If you are planning on applying Intumescent paint well into the fitout phase you are likely to encounter challenges with obstructions, access, QA inspection and the like,
Unfortunately looking at the Intumescent early often means you are having to apply in an environment that is volatile. Hence why less durable Intumescent paints such as water based are often not suitable in a NZ build environment. Solvents, Epoxies and sealers are your best insurance policy to ensure the Intumescent Paint can be applied without risk of failure during
the build.
The reality is that most of NZ is close to the coast & particularly our cities where most large projects are the building site is likely to be exposed to the elements for many months before being fully enclosed. Therefore, although the finished product is going to be in an airtight C1 environment it is more often than not that the building & steel will be exposed to salt air, rain & the like for many months.
Alternatively, the design team and build team could sacrifice programme and allow for Intumescent to be applied in a more optimum condition.
There are great technologies coming available where Intumescent are able to be applied in factory. This provides massive benefits to the project, but needs careful design, methodology and procurement planning to ensure this can be executed well.
Primer concerns:
Sadly, the biggest issue that is happening in the field at present is that blast & primer application is seeing far too many projects that are not up to specification. This then creates massive delays and remedial works on site. There are several stories of entire building lots of steel having to be 100% re-sand blaster & months of delays on primer remedials on site.
The design team and build team need to ensure the specification requirements for blast/ primer are fully understood at the start of the project and remove the risk of shoddy corrosion protection steel arriving on site.
This is a role that Main Contractors need to step up and ensure consideration is given in the procurement phase to ensure a) quality blast/ prime operators are being engaged b) that Intumescent requirements are communicated to all parties c) quality Intumescent applicators are engaged and d) that methodology & programme are given suitable thought & allowance.
Justin McEntyre
Passive Fire Protection SIG Chair 2021/2022
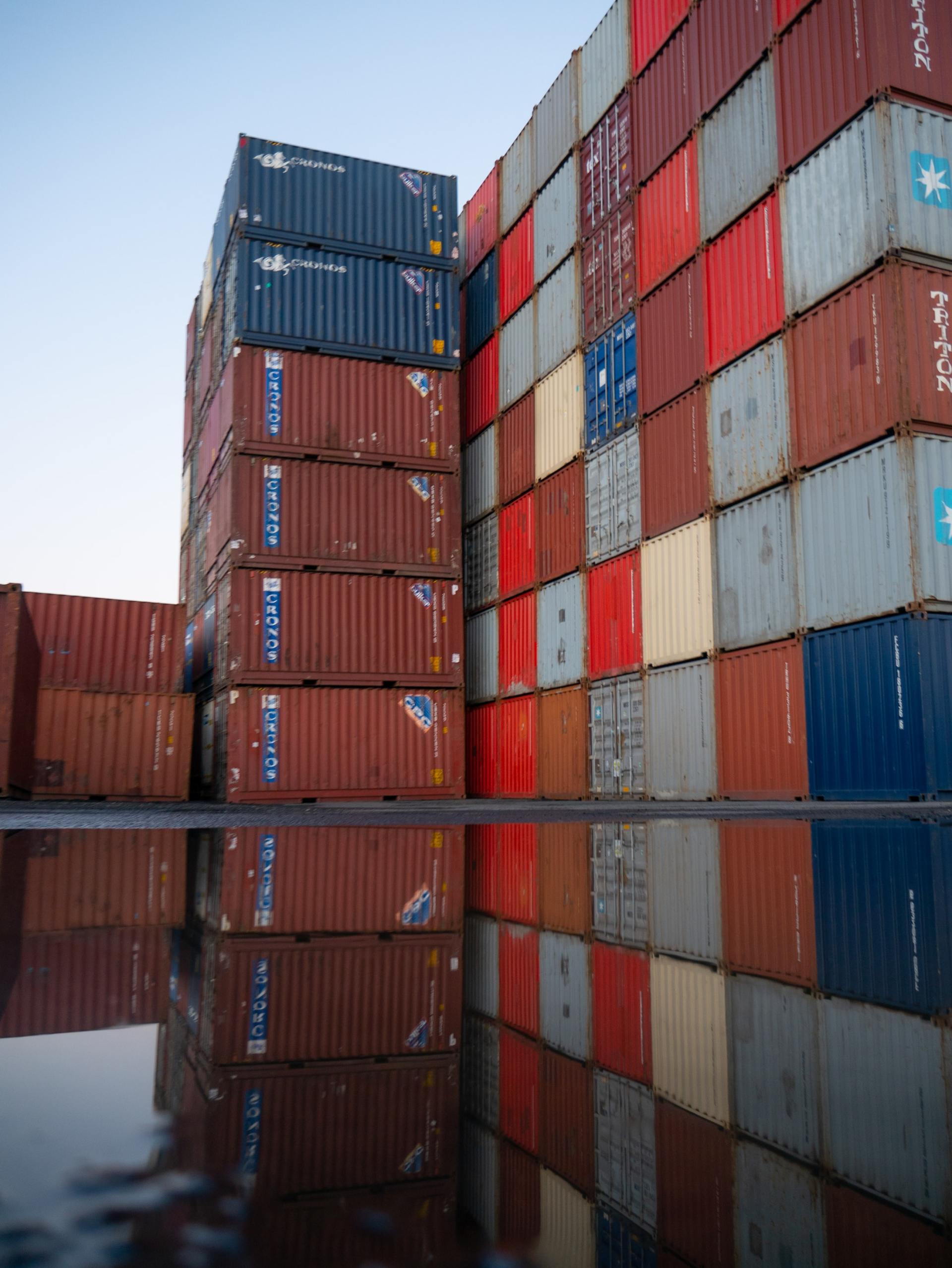
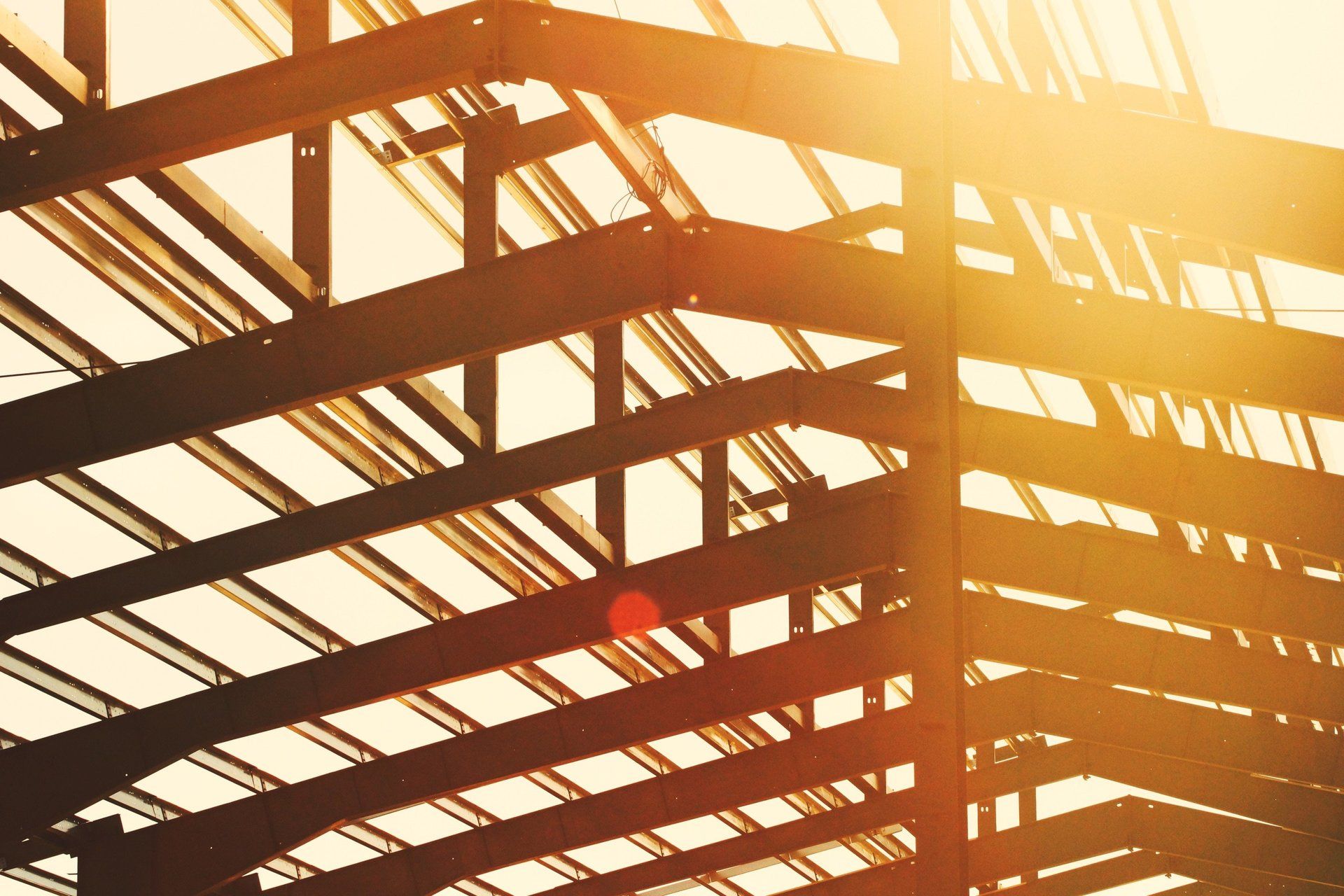
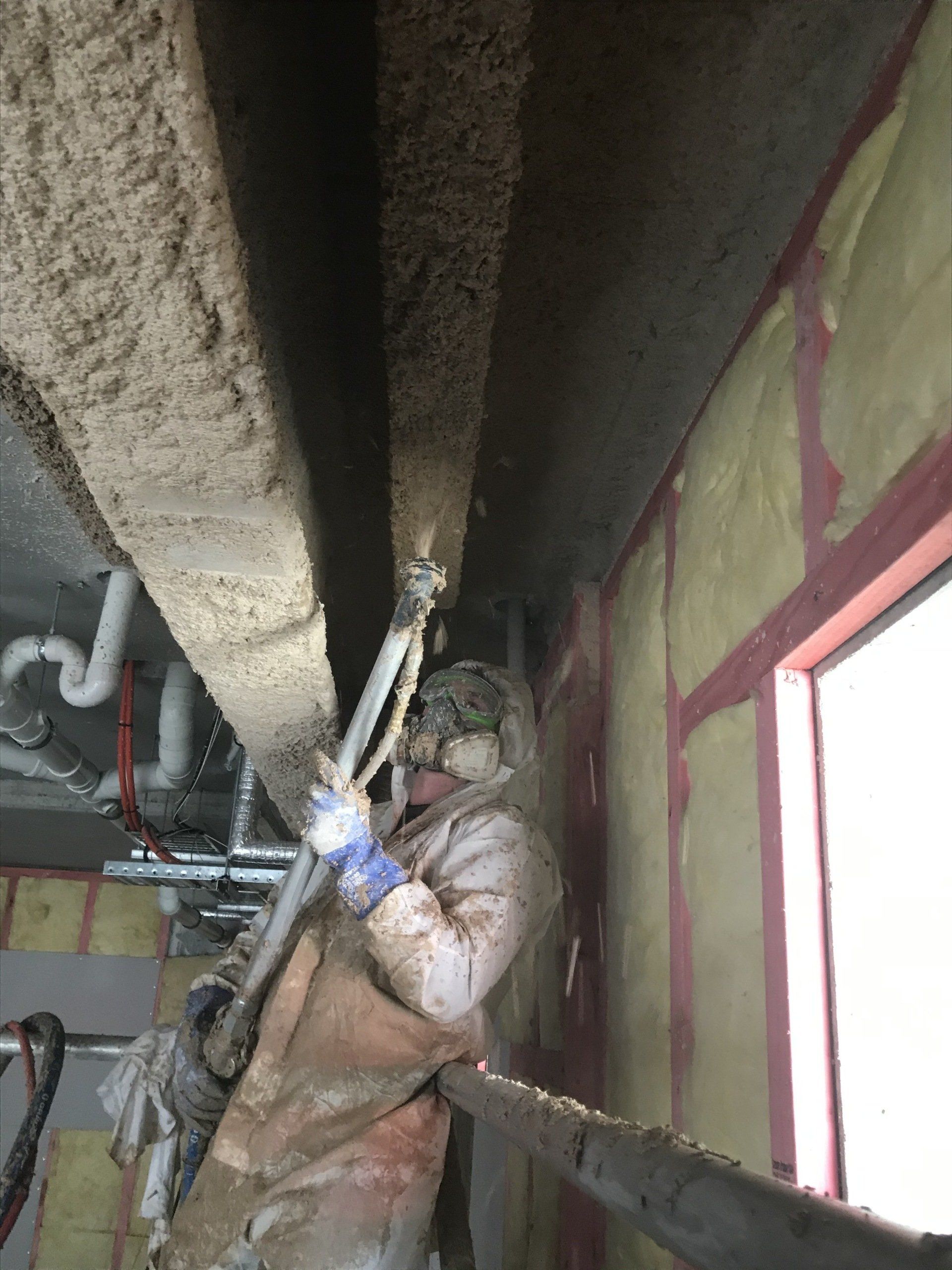