What we do and why we do it!
Kate Franklin Willson • February 9, 2020
The role of the passive fire protection installer
A well designed passive fire protection (PFP) strategy and specification
is not the only thing to think about when planning your building fire protection. Of equal importance is the workmanship and standards of the passive fire installers and team that will maintain the building in the long run.
Passive fire protection
is built into every part of your building in the form of walls, floors, ceilings, beams, columns down to the seals, fire-stops, doors and shutters. It performs two essential functions in the event of a fire:
1.
It keeps your building or asset structurally stable for longer to give people the time to get out safely and can also be great benefit to fire fighters.
2.
Fire protection helps to prevent the spread of fire and smoke within the building or between subdivisions within a single asset, again helping to protect people as well as valuable contents in a building.
Passive Fire design and specification strategies are made up of many elements that together make a critical system. It is important to understand that Installing any single one of these elements without a proper understanding of the overall critical system, can lead to integration errors even when that element is correctly installed. Although the risk of fire cannot be entirely eliminated, the impact that it can have to a building, its contents and those that my be in it, is so damaging that it is important to take every effort to minimise this at every stage of a build.
Fires and smoke are dangerous but they usually become catastrophic when they spread from the room of origin. The point of fire protection is to prevent this spread or, at the very least, delay it. All too often, however, fires do spread, often because of faults with the installation.
Certain elements of PFP construction such as masonry walls or timber or steel structures are likely to remain untouched throughout the life of the structure. They need no maintenance and therefore, the main risks arise if they are not installed correctly to begin with.
Other elements of construction suffer from regular wear & tear are a higher risk factor.
For other areas of construction that are subjected to daily use such as doors, partition walls and shutters, it it necessary to have regular maintenance and to be checked for quality and fire safety standards. Equally, elements that are likely to be altered to allow building services to pass through will suffer damage and require repair. Any new additions to the structure of the building or the internal fixtures must be properly installed and need to have effective fire stopping too.
As most passive fire protection components are hidden in within the building once construction is finished, it is very difficult to check, maintain and repair should there be a problem. It takes skill, experience and competence to accurately identify the fire rating of an element, this is especially necessary in the absence of information and documentation.
Of course sometimes fixing or installing fire stopping measures in older buildings it is necessary and unavoidable especially if the use of the building changes or there are new laws or regulations introduced that change fore safety standards. This can often be carried out by less well qualified facilities management staff than during an initial build, where highly qualified fire installers
with a fresh understanding of the fire strategy may be on hand.
Success lies in the hands of the installer!
Part of the solution to good installation is to get the specification right in the first instance. A comprehensive specification, clearly defined and accompanied by accurate, comparable drawings, goes a long way to mitigating the risk of misunderstanding. Even after handing over comprehensive specification information and clearly communicating the strategy, success still lies in the hands of the installer!
It is not enough to rely solely on the installer’s authorisation. Instead, you should always check that that they have relevant recent experience, and that they can back up their claims with certificates of competence. The things to look for are not just the existence of a certificate, but a relevant, up-to-date accreditation from a recognised organisation. Given the fire risks associated with passive fire protection installation, careful scrutiny of any documentation is critical.
Insisting on certificates of this kind will demonstrate due diligence in the unfortunate event of a fire and gives the highest possible level of confidence that the work will be carried out correctly. Dealing with the damaging effects of fire is bad enough without the additional burden of being the subject of a legal claim.
Small 'simple' repairs can have catastrophic effects on the fire rating
While the fixed structural elements of PFP are of course critically important, they are rarely subject to change during the life of a building. We have established that partition walls and doors are much more prone to be altered or suffer damage through wear and tear than fixed structural elements of PFP, so it is especially important that the people who install or maintain them understand what they are doing. The fundamental objective is to preserve the element’s confirmed fire rating. Small repairs to the beading around the glazing in a fire door can have catastrophic effects on the fire rating, for example, and so it is critical that the installer must appreciate what can and cannot be done.
There is no question that employing third-party certified installers are worth the extra cost for the fire risks they mitigate. Furthermore, installing and maintaining passive fire protection correctly extends their service life. More to the point, retrospective fixes for poorly installed designs are difficult and expensive to fix, adding extra motivation to get it right first time round.
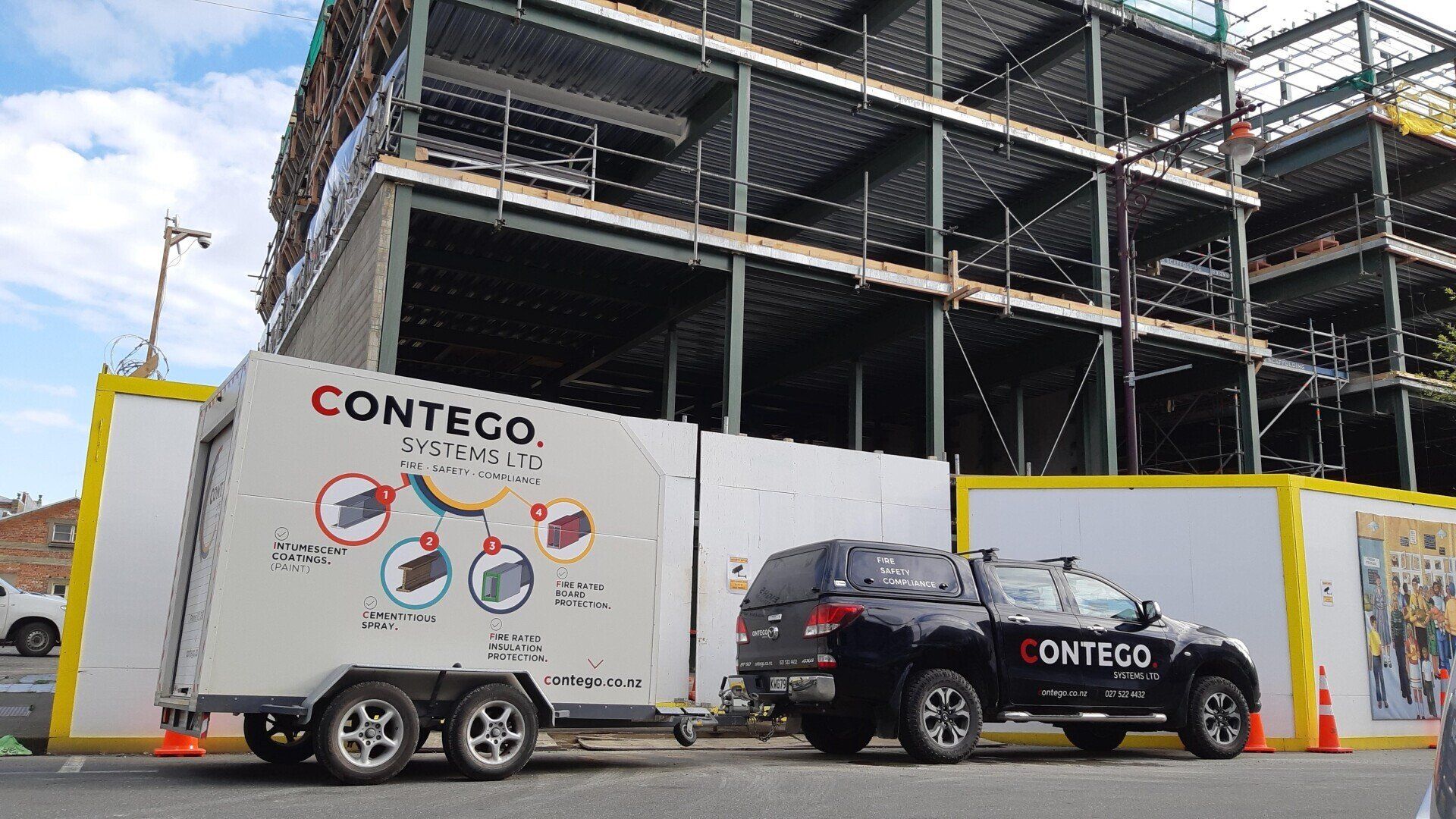
The Passive Fire Protection Intumescent Coating Code of Practice suggests that this should be a collaborative effort between all design consultants to ensure all aspects are considered. This way of thinking is no different to any other collaborative effort in designing a building whereby multiple consultants need to talk & collaborate on a solution.
South Island passive fire protection contractor Contego today announced that it will continue its business expansion by opening a new base in the North Island in December 2021. Located in New Plymouth, the branch is expected to employ 10 persons over the next 24 months. The business currently employs 35 personnel between its bases across the South Island.
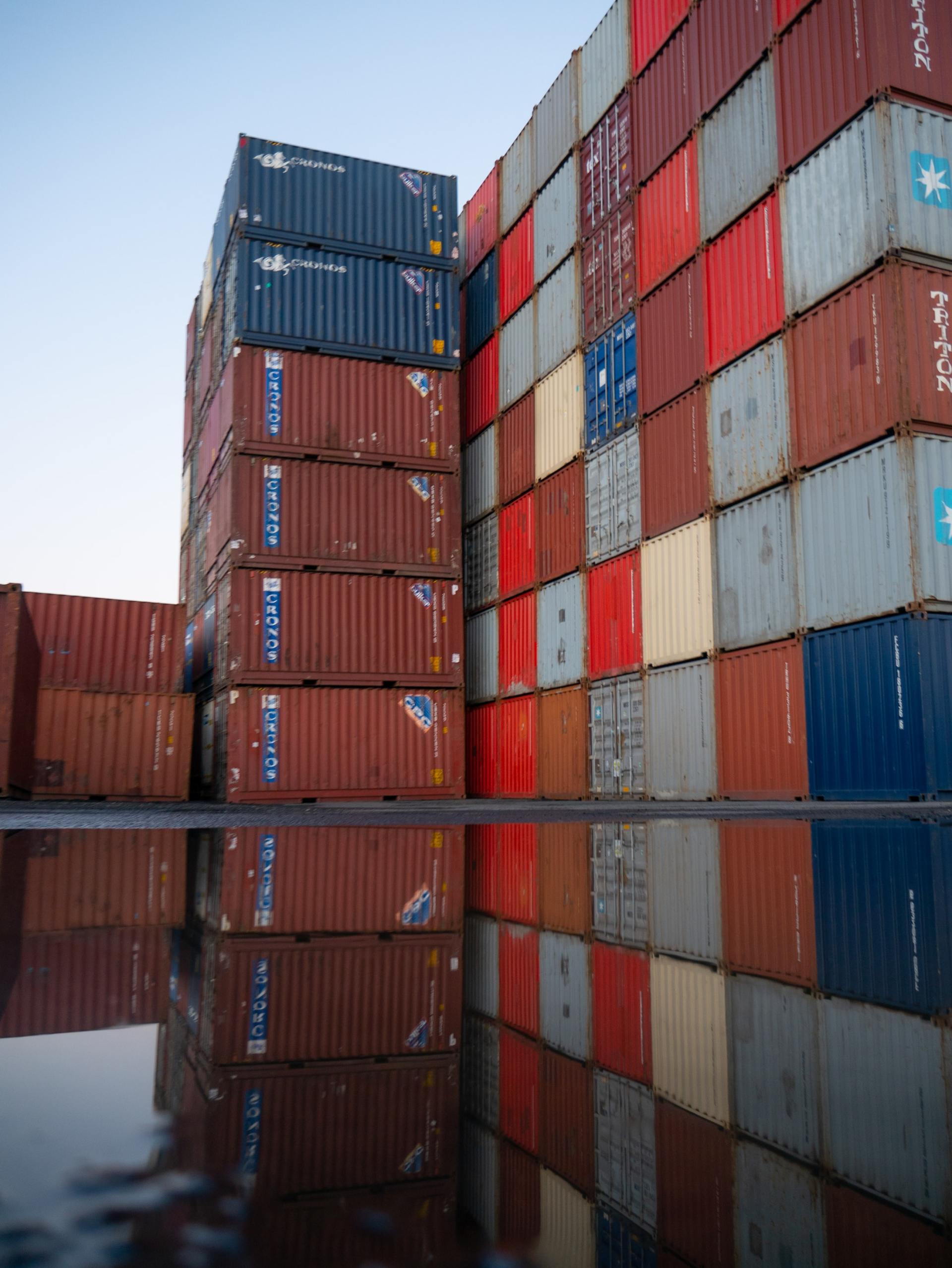
I’m sure I’m not the only one that is experiencing weekly headaches with freight delays and lead time materials. What was once available down the road, can now be a lengthy delay to get a hold of it. The feedback I am getting from suppliers and contractors is that the worst is not over, and we should be planning to deal with this for the remainder of this year.
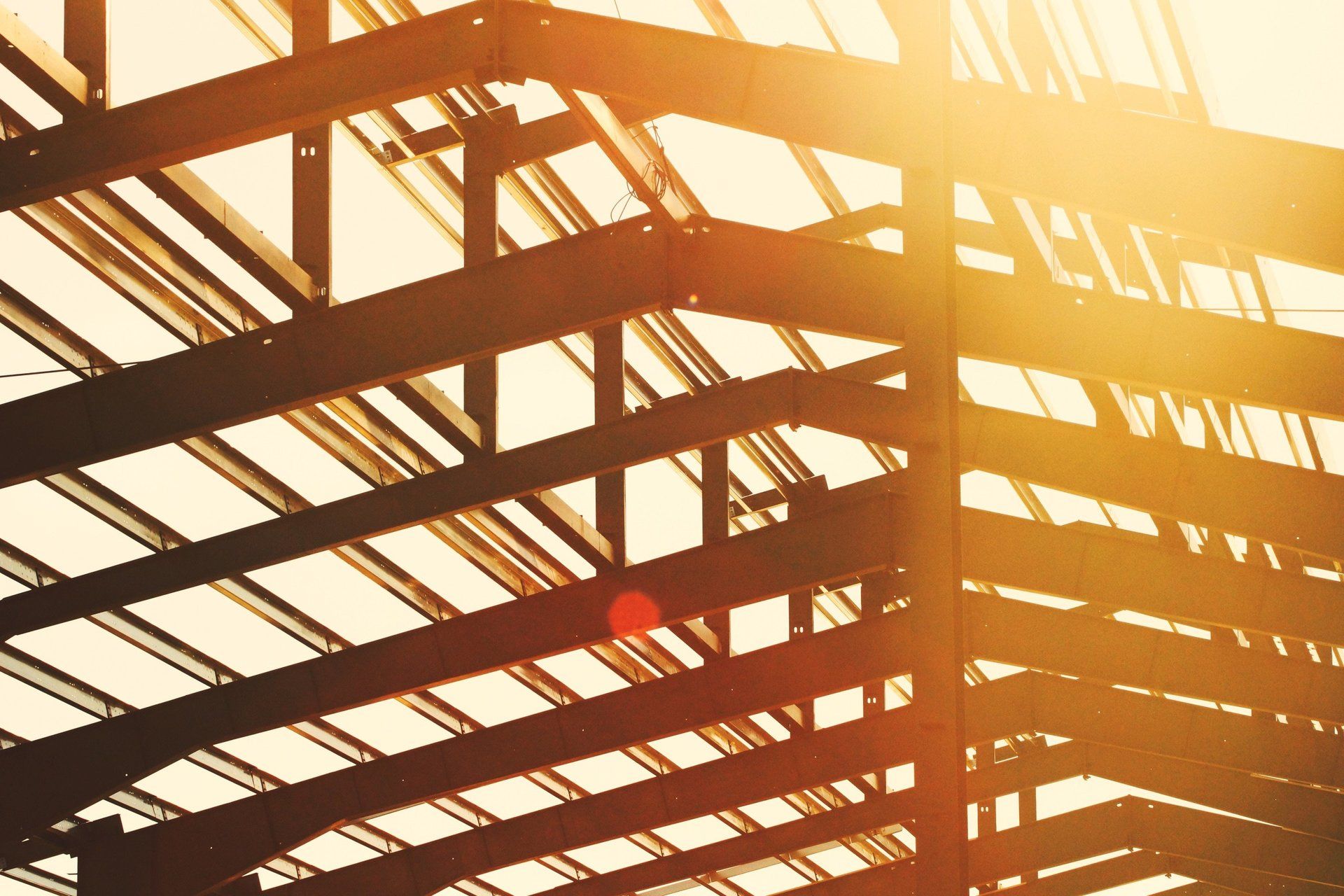
With the current codes of practice and Passive products annual renewal being worked through the issue of Tested vs Assessed is constantly brought up in conversation. NZBC accepts the use of AS4072.1 Assessments as a way of showing compliance as an equal with a tested solution in accordance with AS1530.4.